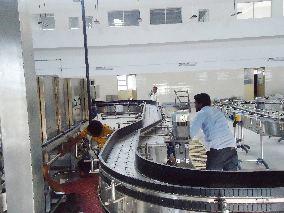
Introduction to Air Conveyors
In the fast-paced world of manufacturing, every second counts. Efficiency is not just a goal; it’s a necessity. Among the many tools and technologies that drive productivity on production lines, air conveyors stand out as unsung heroes. These innovative systems transport materials swiftly and seamlessly using compressed air, revolutionizing how products move through various stages of assembly or packaging.
Imagine reducing manual handling while increasing throughput—all thanks to a system that harnesses the power of air. If you’re curious about how these conveyor systems work and what benefits they offer for your production line efficiency, you’re in the right place. Let’s dive into understanding air conveyors and discover their potential to transform your operations!
Types of Air Conveyors and Their Functions
Air conveyors come in various types, each designed to meet specific operational needs. One common type is the pneumatic conveyor, which utilizes air pressure to move materials efficiently. These are often found in industries like food processing and packaging.
Another popular option is the vacuum conveyor. This system creates a vacuum that draws lightweight items along a designated path. It’s particularly effective for transporting small parts or fragile products without causing damage.
A third variant is the blower-type air conveyor. This system employs high-velocity airflow to push heavier objects down a production line. It’s ideal for moving bulkier goods quickly and effectively.
There are modular air conveyors that can be customized for unique layouts and requirements. Their adaptability allows manufacturers to optimize their workflow easily while enhancing overall productivity.
Benefits of Using Air Conveyors in Production Lines
Air conveyors offer a range of advantages that significantly enhance production line efficiency.
First, they reduce the need for manual handling. This leads to quicker processing times and minimizes worker fatigue.
These systems are also adaptable to various materials, from lightweight packages to delicate items. This versatility makes them ideal for diverse manufacturing environments.
Another benefit is their low energy consumption compared to traditional conveyor systems. Businesses can save on operating costs while maintaining high productivity levels.
Air conveyors operate quietly, contributing to a more pleasant workplace atmosphere. Less noise means better communication among workers and improved focus on tasks.
Additionally, these systems require minimal maintenance because there are fewer moving parts involved. This reliability ensures consistent operation without frequent downtime due to repairs or malfunctions.
Factors to Consider When Choosing an Air Conveyor
When selecting an air conveyor, various factors come into play. First, consider the material being transported. Different products may require specific types of carriers to ensure safe handling.
Next, evaluate the system’s capacity and speed. Your production line’s demands will dictate how much throughput is necessary. Matching these metrics can help maintain efficiency and prevent bottlenecks.
Air quality and environmental conditions are also crucial. Dusty or humid environments might affect performance, so choosing a model built for such conditions is vital.
Don’t overlook energy efficiency either; an eco-friendly option can save costs in the long run while reducing your carbon footprint.
Think about maintenance requirements. Systems that are easier to service will minimize downtime and keep operations running smoothly. By considering these aspects carefully, you’ll find an air conveyor that seamlessly integrates into your production workflow.
Maintenance and Safety Tips for Air Conveyors
Regular maintenance is crucial for the longevity of air conveyors. Start by checking air filters frequently to ensure optimal airflow. Clogged filters can hamper performance and lead to costly downtime.
Inspect hoses and connections for wear or damage. Replace any frayed components immediately, as these can cause leaks that reduce efficiency.
Lubrication is key in maintaining moving parts. Use appropriate lubricants as recommended by the manufacturer to minimize friction and extend service life.
Safety should be a priority in operation. Ensure that all operators are trained on proper usage and emergency protocols. Implementing clear signage around conveyor systems can prevent accidents.
Always keep a fire extinguisher nearby, especially if your production line involves flammable materials. Proper training alongside regular equipment checks helps maintain a safe working environment while ensuring productivity stays high.
Case Studies: Real Life Examples of Improved Efficiency with Air Conveyors
In a beverage bottling plant, the integration of air conveyors reduced product handling time by 30%. By utilizing a streamlined air transport system, bottles moved swiftly from filling stations to packaging areas without manual intervention. This not only sped up the process but also minimized spills and breakage.
Another interesting case was in an automotive parts manufacturing facility. The company replaced traditional conveyor belts with air conveyance systems that accommodated varying part sizes. As a result, they achieved greater flexibility and reduced downtime during product changeovers.
A food processing company saw significant gains as well. Implementing air conveyors allowed for faster transfer of packaged goods through the assembly line. This improved throughput directly impacted their ability to meet customer demand while maintaining quality standards.
These examples showcase how companies across various industries are leveraging air conveyors to enhance productivity and streamline operations effectively.
Conclusion
Understanding Air Conveyors: How They Improve Production Line Efficiency has revealed their vital role in modern manufacturing. These systems streamline operations and enhance productivity through various types tailored to specific tasks. The benefits, from increased speed to reduced labor costs, make air conveyors a valuable investment for any production line.
Choosing the right air conveyor involves considering factors like the type of materials being moved and the layout of your facility. Maintenance is essential for ensuring long-term performance and safety, making regular checks necessary.
Real-life examples illustrate how companies have transformed their efficiency by integrating air conveyors into their processes. These case studies show that with proper implementation, businesses can achieve significant gains.
The adoption of air conveyors represents a step forward in optimizing production lines. By understanding their functionality and advantages, manufacturers can harness this technology to boost overall operational effectiveness.