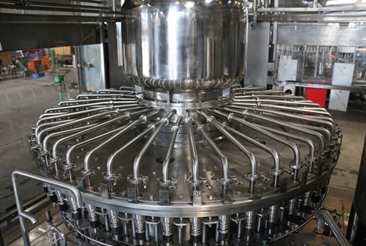
Choosing the right filler machine for your business can feel like navigating a maze. With so many options available, it’s easy to get lost in technical jargon and endless features. But fear not! This ultimate guide is here to help you cut through the noise and make an informed decision tailored to your unique needs.
Whether you’re filling bottles, pouches, or jars, understanding what type of filler machine suits your product best is crucial. The right choice can boost efficiency, enhance productivity, and ultimately drive profitability for your operations.
Get ready as we dive into everything you need to know about selecting the perfect filler machine that aligns with your business goals. Let’s embark on this journey together and ensure you find a solution that works seamlessly for you!
Understanding Your Business Needs
Understanding your business needs is the first step in selecting a filler machine. Each operation has its own requirements based on product type, volume, and packaging style.
Start by evaluating what you are filling. Is it liquid, powder, or granulated? Different products necessitate different machines designed to handle specific consistency and flow characteristics.
Next, consider your production volume. Are you looking for high-speed output or lower quantities with more flexibility? A machine that aligns with your scale will enhance efficiency without causing bottlenecks.
Don’t forget about future growth. Choose a filler that can adapt as your business expands or pivots to new offerings. This foresight saves time and money down the line.
Take into account any regulatory requirements specific to your industry. Compliance plays an essential role in ensuring quality control and consumer trust.
Types of Filler Machines
Filler machines come in various types, each designed for specific applications. Understanding these can help you make the right choice for your business.
Gravity fillers are popular for thin liquids. They utilize gravity to dispense products into containers. This method is straightforward and effective but may not be suitable for thick or viscous substances.
Piston fillers offer versatility, accommodating a range of viscosities. They use a piston mechanism to draw liquid from a reservoir and push it into the container. This makes them ideal for both liquids and pastes.
Vacuum fillers work well with foamy or delicate products by creating a vacuum that draws the product into containers without introducing air bubbles.
Ampoule fillers specialize in filling small glass vials often used in pharmaceuticals and cosmetics, ensuring precision with every fill. Each type has its unique strengths tailored to different industry needs.
Factors to Consider When Choosing a Filler Machine
When selecting a filler machine, the first factor to consider is your product type. Liquid, powder, or granules each require specialized machines.
Next, assess your production volume. High-output operations need robust machinery that can handle rapid cycles without compromising quality.
Speed and accuracy are also vital. Look for equipment that balances both to minimize waste and meet customer expectations.
Another consideration is flexibility. If you plan to expand your product line in the future, choose a machine that can adapt easily to different filling requirements.
Don’t overlook space limitations in your facility. Choose a compact design if floor space is at a premium.
Evaluate ease of use and maintenance needs. User-friendly interfaces save training time while reliable support ensures minimal downtime during repairs or adjustments.
Popular Brands and their Features
When it comes to filler machines, certain brands stand out for their reliability and innovative features.
Bosch is known for its advanced technology, offering precision filling with minimal downtime. Their machines are designed for high-speed production while ensuring consistent quality.
Next up is Accutek Packaging Equipment. They provide a diverse range of fillers suitable for various industries—from liquids to granules. Their customizable options make them popular among businesses looking to scale operations.
Another noteworthy brand is KHS. With a focus on sustainability, KHS designs machines that reduce waste and energy consumption without compromising performance.
We have Inline Filling Systems, which excels in user-friendly designs and quick changeovers between products—ideal for companies needing flexibility in their production lines.
Maintenance and Repair Costs
Maintenance and repair costs are crucial considerations when selecting a filler machine. Regular upkeep ensures optimal performance, but these expenses can vary significantly based on the type of machine.
Some machines require minimal maintenance, leading to lower long-term costs. Others may have complex components that demand more frequent servicing or specialized technicians.
Consider warranty options offered by manufacturers. A solid warranty can mitigate unexpected repair expenses early on.
It’s also wise to factor in downtime during repairs. If a machine fails, how quickly can it be fixed? This could translate into lost productivity and revenue for your business.
Look for machines with readily available parts. Hard-to-find components often lead to higher repair bills and longer wait times.
Tips for Maximizing Efficiency and Productivity with a Filler Machine
To maximize efficiency with a filler machine, start by ensuring it’s properly calibrated. Regular adjustments can prevent inconsistencies that waste materials and time.
Next, invest in training your team. A skilled operator understands the machine’s nuances, leading to smoother operations and fewer errors.
Maintenance routines are crucial. Schedule regular checks to keep components functioning optimally. This minimizes downtime caused by unexpected repairs.
Utilizing automation features can also enhance productivity. Look for machines equipped with advanced technology that streamlines processes and reduces manual intervention.
Monitor performance metrics consistently. Analyze data to identify bottlenecks or areas needing improvement, allowing you to make informed decisions that boost overall output.
Conclusion
Selecting the right filler machine for your business is a significant decision that can impact your operations, efficiency, and ultimately, your bottom line. By understanding your specific needs and the various types of machines available, you can make an informed choice that aligns with your production goals.
It’s important to consider factors like speed, accuracy, and ease of use when evaluating different options. Popular brands often come with distinctive features that cater to diverse market demands. Staying mindful of maintenance and repair costs will ensure long-term sustainability for any investment you make.
Maximizing efficiency should always be a priority once you’ve made your selection. Implementing best practices in operation can enhance productivity significantly.
With careful consideration and research tailored to your unique requirements, you’re well on your way to choosing a filler machine that not only meets but exceeds expectations—empowering growth within your business journey.