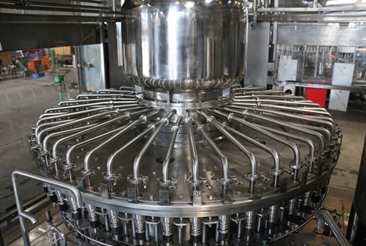
Welcome to the exciting world of filling machines, where precision meets efficiency in the art of packaging. Join us on a journey through time as we explore how these ingenious devices have evolved from humble manual systems to advanced automated processes. Get ready to dive into the evolution of filling machines and discover how technology has revolutionized the way products are filled and packaged. Let’s unravel the fascinating story of innovation and progress in the realm of filling equipment!
The Early Days of Filling: Manual Processes
In the early days of manufacturing, filling containers was a labor-intensive task that required manual precision. Workers would meticulously pour and measure liquids or powders into bottles, jars, or other packaging by hand. This process was time-consuming and prone to human error.
Manual filling processes often relied on simple tools like funnels and measuring cups to ensure accuracy. Each container had to be filled individually, leading to inefficiencies in production lines. Despite the challenges, these manual methods were the foundation of modern filling technology.
As industries evolved and demand increased, there arose a need for more efficient solutions. Innovations in engineering led to the development of semi-automated filling machines that could partially automate the filling process. These advancements marked a significant step towards streamlining production and improving consistency in product packaging.
The transition from manual to semi-automated processes revolutionized manufacturing operations by enhancing speed, accuracy, and reliability. It laid the groundwork for further advancements in automation that would shape the future of filling machines as we know them today.
Advancements in Technology: Semi-Automated Filling Machines
Advancements in technology have revolutionized the way filling machines operate. Semi-automated filling machines represent a significant leap forward from manual processes, offering increased efficiency and accuracy in product packaging. These semi-automated systems combine the best of both worlds by integrating some automated features while still requiring human intervention for certain tasks.
Semi-automated filling machines streamline production processes, reducing the risk of errors and ensuring consistent fill levels across products. With the ability to handle a wide range of container sizes and types, these machines offer versatility to manufacturers looking to optimize their packaging operations.
By incorporating innovative technologies such as programmable logic controllers (PLCs) and touch screen interfaces, semi-automated filling machines provide user-friendly operation and enhanced control over the filling process. This level of automation not only improves productivity but also allows for quick changeovers between different products or packaging formats.
Semi-automated filling machines serve as a bridge between traditional manual methods and fully automated systems, offering companies a cost-effective solution to enhance their production capabilities without committing to full automation at once.
The Rise of Automation: Fully Automated Filling Machines
The rise of automation in the filling industry has revolutionized production processes. Fully automated filling machines have streamlined operations, increasing efficiency and accuracy. These advanced machines can precisely fill a wide range of products at high speeds, minimizing human error.
By incorporating sensors and robotics, fully automated filling machines ensure consistent fill levels and reduce product waste. The integration of smart technology allows for real-time monitoring and adjustments to optimize performance.
With user-friendly interfaces and programmable settings, operators can easily set up the machine for different products with minimal downtime. This versatility makes fully automated filling machines adaptable to various industries, from food and beverage to pharmaceuticals.
The evolution towards fully automated filling machines signifies a shift towards enhanced productivity and quality control within manufacturing processes.
Benefits and Limitations of Automated Filling Machines
Automated filling machines offer a range of benefits that have revolutionized the manufacturing industry. They enhance efficiency by significantly reducing human error and increasing production speed. With precise measurements and consistent output, automated fillers ensure product quality and uniformity, resulting in higher customer satisfaction.
Additionally, automated systems can handle a variety of products with different viscosities, textures, and packaging sizes without requiring extensive reconfiguration. This versatility allows manufacturers to streamline their processes and adapt quickly to changing market demands. Moreover, automation reduces labor costs over time as fewer employees are needed to operate the machinery.
On the flip side, one limitation of automated filling machines is the initial investment required for installation and maintenance. While these systems offer long-term cost savings, some businesses may find it challenging to justify the upfront expenses associated with implementing automation technology. Additionally, complex products or unique packaging requirements may not always be compatible with standard automated solutions.
Nonetheless, as technology continues to advance, we can expect these limitations to diminish while the benefits of automated filling machines become even more pronounced in various industries worldwide.
Future Trends and Innovations in Filling Machine Technology
As technology continues to advance at a rapid pace, the future of filling machine technology looks promising. One major trend on the horizon is the integration of artificial intelligence and machine learning algorithms into filling machines. This will enable them to optimize production processes in real-time, leading to increased efficiency and accuracy.
Another exciting innovation is the development of smart sensors that can detect inconsistencies or errors during the filling process. By utilizing these sensors, manufacturers can ensure consistent product quality while minimizing waste.
Furthermore, 3D printing technology may revolutionize how filling machines are constructed in the future. This could lead to more customizable and cost-effective solutions for various industries.
Additionally, there has been a growing focus on sustainability in recent years. Future filling machines are likely to be designed with eco-friendly materials and energy-efficient mechanisms to reduce their environmental impact.
As we look ahead to the future of filling machine technology, it’s clear that there are countless possibilities for innovation and improvement in this field.
Conclusion
The evolution of filling machines from manual to automated processes has revolutionized the manufacturing industry. The journey from hand-operated systems to fully automated equipment has significantly increased efficiency, accuracy, and production rates. While there are benefits and limitations to each type of filling machine, it’s clear that automation is the way forward for businesses looking to streamline their operations.
As technology continues to advance, we can expect even more innovations in filling machine technology. From improved precision and customization capabilities to enhanced data analytics and connectivity features, the future of filling machines is bright. Companies that invest in cutting-edge automation solutions will undoubtedly stay ahead of the curve and maximize their competitive advantage in the market.
The evolution of filling machines showcases how innovation drives progress in manufacturing. By embracing new technologies and adapting to changing demands, businesses can optimize their production processes for greater success. As we look towards the future, one thing is certain: automated filling machines will continue to play a pivotal role in shaping the industry landscape for years to come.