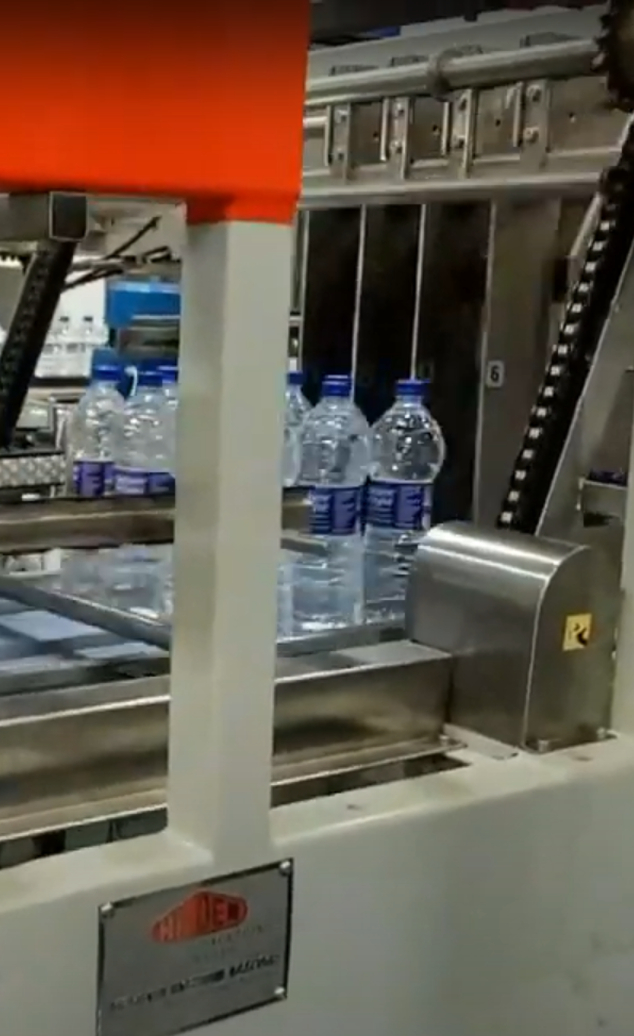
Introduction to liquid filling machines
In the fast-paced world of food and beverage production, efficiency is key. One of the unsung heroes behind seamless operations is the liquid filling machine. These machines have come a long way from their humble beginnings, evolving into sophisticated systems that not only enhance productivity but also ensure product quality and consistency. As consumer demands rise and market competition intensifies, businesses are turning to innovative filling technologies to stay ahead.
The latest innovations in liquid filling machines for the food and beverage industry are transforming how products reach consumers. From juice manufacturers to sauce producers, automated solutions are revolutionizing processes, making them faster and more precise than ever before. Let’s dive into what makes these advancements so exciting!
Types of liquid filling machines:
Liquid filling machines come in various forms, each designed for specific applications. Understanding these types can help manufacturers choose the right fit.
Gravity fillers are among the simplest and most economical options. They rely on gravity to allow liquids to flow into containers, making them ideal for low-viscosity products like water or juice.
Piston fillers utilize a piston-driven mechanism that provides precision for thicker liquids such as sauces or creams. This type allows for consistent volume control and is great for high-viscosity materials.
Overflow fillers ensure accurate fill levels by allowing excess liquid to overflow back into the reservoir. This method is particularly useful in maintaining uniform fills across bottles.
Vacuum fillers create a vacuum within containers, drawing in liquid with accuracy. They work well with foamy or aerated liquids while minimizing spillage during the filling process. Each type has its unique advantages tailored to specific industry needs.
A. Gravity fillers
Gravity fillers are among the simplest types of liquid filling machines. They operate on a fundamental principle: gravity does the heavy lifting. This makes them ideal for filling liquids that flow easily, such as water or juice.
The design typically features a hopper where the liquid is stored before it flows into containers below. Because they rely on gravity, these fillers tend to be cost-effective and easy to maintain.
While they’re not suited for thicker products, their efficiency in handling low-viscosity liquids can’t be overlooked. Many manufacturers appreciate how quickly they can fill bottles with minimal setup time.
Additionally, gravity fillers offer flexibility in container sizes and shapes, making them versatile assets on production lines. Industries looking for straightforward solutions often find this type of machine meets their needs perfectly.
B. Piston fillers
Piston fillers are a popular choice in the food and beverage industry. They excel at dispensing thick, viscous liquids as well as free-flowing products. This versatility makes them invaluable for companies producing sauces, syrups, or even cosmetic items.
The operation is straightforward. A piston draws liquid into a cylinder and then pushes it out through a nozzle during filling. This mechanism ensures precise measurements with every cycle.
One of the standout features is their adaptability to varying container sizes. Piston fillers can easily switch between different bottle shapes without major adjustments, enhancing production efficiency.
Moreover, they minimize waste by offering accurate fills that reduce spillage. The design allows for easy cleaning and maintenance too—an essential factor in adhering to hygiene standards within the industry.
With increasing demand for high-quality packaging solutions, piston fillers stand out as reliable machinery suited for modern production lines.
C. Overflow fillers
Overflow fillers are a popular choice in the food and beverage industry for their ability to deliver consistent, accurate fills. This type of filling machine operates by allowing liquid to flow until it reaches a predetermined level. The excess then overflows back into the reservoir, ensuring each container receives an exact amount.
These machines excel with thin or foamy liquids like juices and sauces. Their design minimizes spillage, which is crucial for maintaining cleanliness and reducing waste during production.
Moreover, overflow fillers can handle various container shapes and sizes without requiring significant adjustments. This versatility makes them ideal for manufacturers looking to streamline operations while maintaining quality standards.
With advancements in technology, modern overflow fillers feature enhanced sensors that monitor fill levels more precisely than ever before. As such innovations emerge, they keep pushing the boundaries of what’s possible within this essential segment of packaging machinery.
D. Vacuum fillers
Vacuum fillers are a game-changer in the liquid filling landscape. They operate by creating a vacuum that draws liquid into the container, ensuring precise fills with minimal spillage.
These machines excel in handling viscous liquids and products that require careful treatment during packaging. The technology minimizes air pockets, preserving product integrity and extending shelf life.
Versatility is another advantage of vacuum fillers. They can easily adapt to different container shapes and sizes, making them ideal for diverse food and beverage applications.
Moreover, their efficiency contributes to faster production rates without compromising accuracy. Businesses can scale up operations while maintaining quality standards.
With continuous advancements, manufacturers are enhancing vacuum filler designs to further streamline processes. This innovation not only boosts productivity but also meets the evolving needs of the industry.
Benefits of using automated liquid filling machines in the food and beverage industry
Automated liquid filling machines revolutionize the food and beverage sector by enhancing efficiency. With faster fill rates, businesses can boost production without sacrificing quality.
Consistency is another key advantage. These machines ensure uniform fills across every bottle or container. This reliability builds trust with consumers who expect their products to meet specific standards.
Additionally, automation reduces labor costs. By minimizing manual intervention, companies can allocate resources more effectively while maintaining a safe working environment.
Flexibility is also a crucial benefit. Modern systems easily adapt to various product types and packaging formats, making it simpler for manufacturers to diversify their offerings.
Automated filling machines contribute to improved hygiene practices in production lines. They are designed for easy cleaning and sanitization, which is vital in the food industry where safety regulations are stringent.
Latest innovations in liquid filling technology:
The food and beverage industry is witnessing remarkable advancements in liquid filling technology. High-speed and precision filling capabilities are at the forefront, enabling manufacturers to boost productivity without compromising on quality. These machines can now fill a variety of container sizes with unmatched accuracy.
Integration with other packaging equipment has transformed production lines into seamless operations. Liquid fillers now work harmoniously alongside labeling, capping, and packing systems, creating an efficient workflow that reduces downtime.
Advanced control systems play a crucial role in enhancing efficiency. They allow for real-time monitoring and adjustments, ensuring optimal performance throughout the filling process. With features like touch-screen interfaces and data analytics, operators can easily manage complex tasks while minimizing human error.
These innovations not only improve operational capacity but also enhance product safety by implementing more stringent controls during the filling process.
B. Integration with other packaging equipment
Integration with other packaging equipment has become a game changer for the food and beverage industry. Liquid filling machines now seamlessly connect with labeling, capping, and even palletizing systems. This creates a streamlined workflow that enhances productivity.
Imagine an assembly line where liquid filling occurs simultaneously with bottle capping or labeling. This reduces downtime and ensures consistency in operations. By minimizing manual handling, companies can also significantly reduce the risk of contamination.
Advanced software solutions support this integration, allowing real-time monitoring and adjustments across all machinery involved in the packaging process. Data from various systems can be analyzed to optimize performance continuously.
Moreover, flexible configurations enable manufacturers to adapt quickly to new products or changes in production volume without major disruptions. The result is not just efficiency but also improved product quality delivered faster to market.
C. Advanced control systems for increased efficiency and accuracy
Advanced control systems have revolutionized the way liquid filling machines operate. These sophisticated technologies allow for real-time monitoring and adjustments during the filling process.
With precision sensors and smart algorithms, these systems ensure that each bottle or container receives the exact amount of product every time. This minimizes waste and reduces the likelihood of costly errors.
Moreover, advanced control systems can integrate seamlessly with production lines. They communicate with other machinery to optimize workflow and enhance overall efficiency.
Operators benefit from user-friendly interfaces that provide instant feedback on performance metrics. This empowers them to make informed decisions quickly.
As a result, businesses not only boost productivity but also maintain high quality standards in their products. The shift towards automation has never been more evident, making these innovations crucial for success in today’s competitive market.
Case studies of successful implementation of
Case studies showcasing successful implementation of liquid filling machines can provide invaluable insights into the tangible benefits these innovations bring to the food and beverage industry. One notable example is a leading juice manufacturer that adopted high-speed gravity fillers for its production line. By streamlining their operations, they experienced a significant reduction in bottling time while maintaining product quality. The transition not only improved efficiency but also allowed them to meet rising consumer demand without compromising on freshness.
Another case involves a premium wine producer that integrated piston fillers with advanced control systems into their packaging process. This technology enabled precise measurements and minimized waste during filling, resulting in cost savings and higher margins. The seamless integration with other machinery further enhanced their overall productivity, allowing them to focus more on expanding their product range.
Moreover, an innovative beverage startup implemented vacuum filling technology within its plant. This method ensured that even highly viscous liquids were filled accurately without air entrapment, preserving flavor integrity. As a result, they gained recognition for both quality and consistency in a competitive market.
These real-world examples illustrate how embracing the latest innovations in liquid filling machines can lead to remarkable improvements across various sectors of the food and beverage industry. Companies not only enhance operational efficiency but also elevate customer satisfaction through better product delivery.