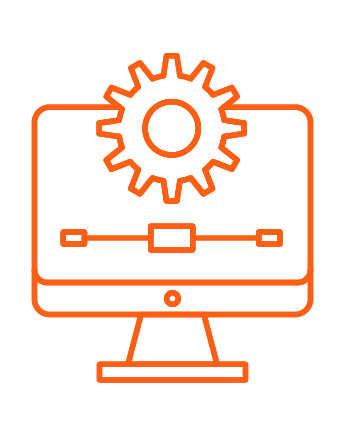
Introduction to Fully Automatic Rinsing, Filling, and Capping Machines
When it comes to packaging liquids, efficiency and accuracy are paramount. Enter the world of fully automatic rinsing, filling, and capping machines—an innovative solution that revolutionizes how products are prepared for distribution. These high-tech marvels streamline the entire process, from cleaning containers to sealing them tight. But how do they work? Understanding their operation can unlock significant advantages for manufacturers across various industries. Let’s delve into the fascinating mechanics behind these machines and explore why they have become essential tools in modern production lines.
The Rinsing Process and its Importance
The rinsing process is a critical step in the packaging line. It ensures that containers are free from contaminants before they’re filled with products. This stage prevents any unwanted residues from affecting product quality.
Containers, whether glass or plastic, must be thoroughly cleaned. Rinsing removes dust, dirt, and chemical residues that may remain after manufacturing. A clean container not only enhances shelf life but also improves consumer safety.
Automation plays a vital role here. Fully automatic rinsing machines use high-pressure jets of water or cleaning solutions to ensure complete cleanliness. These systems can handle various container shapes and sizes efficiently.
By investing in advanced rinsing technology, companies minimize human error and improve consistency across their production lines. This attention to detail reflects positively on brand reputation and customer trust.
The Filling Process: Types of Fillers and Their Functions
The filling process is a critical stage in packaging. It ensures products are dispensed accurately into containers, maintaining quality and safety.
There are various types of fillers used in this process. Volumetric fillers measure the volume of liquid being filled, providing precise amounts every time. They’re ideal for beverages and sauces.
Then we have gravimetric fillers that weigh the product before dispensing it into containers. This method is beneficial for powders or granular materials, ensuring consistency with every fill.
Piston fillers utilize a piston mechanism to push product through the nozzle. They excel with thicker liquids or pastes like creams and gels.
Counter-pressure fillers are perfect for carbonated drinks. They help maintain carbonation levels during filling by equalizing pressure between the bottle and filler.
Each type serves specific needs within different industries, reinforcing their importance in efficient production lines.
Capping Techniques: Manual vs Automatic
Capping techniques play a crucial role in ensuring product integrity. Manual capping involves operators applying caps by hand. This method can be time-consuming and often relies on human precision.
On the other hand, automatic capping machines streamline this process. They utilize advanced technology to precisely place and secure caps quickly and efficiently. These machines are designed for high-speed production lines, reducing labor costs significantly.
Automatic systems also minimize the risk of contamination or inconsistent sealing that may occur with manual methods. With features like torque control, they ensure each cap is tightened just right.
Choosing between manual and automatic capping depends on production volume and budget considerations. For smaller businesses, manual capping might suffice initially. However, as demand grows, investing in automation becomes more appealing to enhance productivity and maintain quality standards.
Advantages of Fully Automatic Rinsing, Filling, and Capping Machines
Fully automatic rinsing, filling, and capping machines offer significant advantages for manufacturers. They enhance productivity by streamlining processes that would otherwise require multiple manual steps.
These machines are designed for precision. Accurate measurements reduce waste and ensure consistent product quality. This reliability is crucial in industries where even minor deviations can affect compliance or customer satisfaction.
Flexibility is another key benefit. Many models accommodate various container sizes and types, making it easier to adapt to changing production needs without extensive reconfiguration.
Moreover, automation reduces labor costs over time. With fewer workers needed for repetitive tasks, companies can allocate resources more strategically.
The integration of advanced technology enhances monitoring capabilities. Real-time data allows operators to quickly identify issues and make adjustments on the fly, ensuring smooth operations throughout the production cycle.
Industries that Benefit from these Machines
Numerous industries experience significant advantages from fully automatic rinsing, filling, and capping machines. The beverage sector stands out as a primary beneficiary. These machines streamline production processes by ensuring precise fills and secure caps on bottles.
The pharmaceutical industry also relies heavily on these systems. Here, accuracy is crucial to maintain product integrity and safety standards. Automatic machines help prevent contamination during the filling process.
Cosmetics manufacturers are another key player. With various bottle shapes and sizes, these machines adapt effortlessly while maintaining high efficiency levels.
Food packaging companies benefit too, especially in sauces or liquid products where hygiene is vital. Fully automatic systems ensure compliance with health regulations while maximizing throughput.
In essence, any sector that requires reliable bottling solutions can see enhanced productivity through the implementation of fully automatic rinsing, filling, and capping technologies.
Maintenance and Troubleshooting Tips
Regular maintenance is crucial for the longevity of fully automatic rinsing, filling, and capping machines. Schedule routine inspections to check for wear and tear on essential components. Lubricate moving parts to minimize friction.
Keep the machine clean. Residues can lead to malfunctions over time. Utilize appropriate cleaning agents that won’t damage sensitive machinery.
When troubleshooting, start with simple checks first. Ensure power supply connections are secure and inspect fuses if issues arise.
Monitor fluid levels closely. Low liquids might cause inconsistent filling or rinsing problems. Adjust settings based on product viscosity as well.
Don’t overlook software updates either; they can resolve bugs and enhance performance features seamlessly. Always refer to the manufacturer’s manual for specific guidelines tailored to your model’s needs when in doubt about repairs or adjustments needed.
Conclusion
Fully automatic rinsing, filling, and capping machines are vital components in modern production lines. These systems streamline the packaging process across various industries, ensuring efficiency and consistency. By automating these crucial steps, businesses can enhance productivity while minimizing human error.
Understanding how fully automatic rinsing, filling, and capping machines work helps companies choose the right equipment for their needs. The rinsing process ensures cleanliness; different fillers accommodate a range of liquids; and innovative capping techniques secure products effectively.
With numerous advantages such as increased speed and reduced labor costs, it’s clear why many manufacturers opt for fully automatic systems. Industries like food and beverage, pharmaceuticals, cosmetics, and chemicals have all benefited from this technology.
To maintain optimal performance of these machines requires regular maintenance practices along with troubleshooting tips to address potential issues quickly. This knowledge empowers teams to keep production running smoothly without unnecessary downtime.
Investing in fully automatic rinsing, filling, and capping machines is a strategic move that can lead to higher profitability and improved product quality in today’s competitive market landscape.