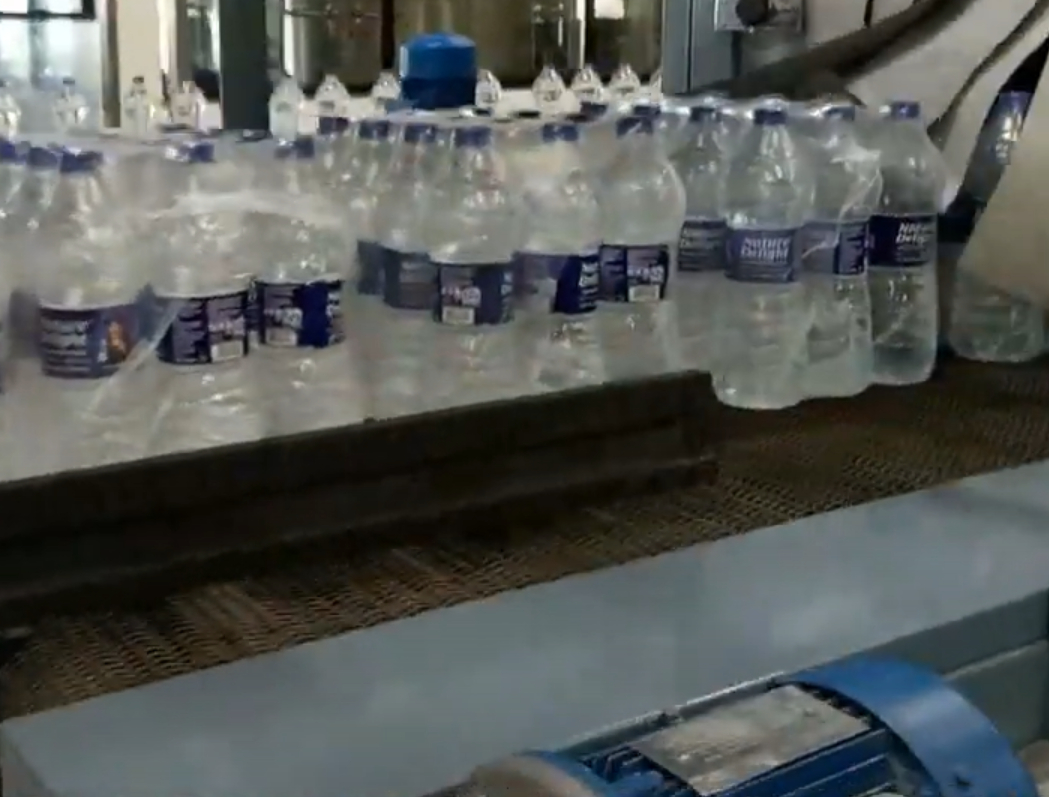
Introduction to Filling Mechanisms
When it comes to filling products, the choice of mechanism can make all the difference. Whether you’re bottling sauces, cosmetics, or pharmaceuticals, the right filling machine ensures efficiency and precision. But with so many options available, how do you decide?
In this blog post, we dive into three popular filling mechanisms: gravity fillers, pressure fillers, and piston fillers. Each has its unique strengths and ideal applications. By comparing these methods side by side, we’ll help you uncover which one is best suited for your business needs. Let’s explore the ins and outs of these systems to empower your decision-making process!
Gravity Fillers: How They Work and Their Advantages
Gravity fillers operate on a simple yet effective principle. They harness the natural force of gravity to dispense liquids into containers. The process begins when the product flows from a storage tank through a valve, allowing it to fill bottles or jars below.
One notable advantage of gravity fillers is their versatility. They can handle various liquid viscosities, making them suitable for products ranging from water to thicker sauces.
These systems are often straightforward in design, which means they require less maintenance compared to more complex filling machines. This simplicity also translates into lower operational costs over time.
Moreover, gravity fillers provide consistent fills with minimal foaming or splashing, ensuring that your products maintain quality and integrity during packaging. Their ease of use makes them an attractive option for small and medium-sized businesses looking to streamline production without breaking the bank.
Pressure Fillers: The Science Behind Them and Their Benefits
Pressure fillers operate on a straightforward principle: using air pressure to transfer liquid into containers. This method is particularly effective for thicker liquids or those with varying viscosities, as the controlled force ensures consistent fills.
One significant advantage of pressure filling is speed. These machines can fill multiple containers simultaneously, drastically reducing production time. The automation in this process also minimizes human error, resulting in more accurate fills and less waste.
Another benefit lies in their adaptability. Pressure fillers can handle various container shapes and sizes without requiring extensive adjustments. This versatility makes them ideal for businesses looking to diversify product lines without investing heavily in new equipment.
Additionally, pressure filling is known for maintaining product integrity. Since it reduces exposure to open air during the filling process, it helps preserve flavor and freshness—an essential factor for many food and beverage manufacturers seeking quality assurance.
Piston Fillers: A Detailed Look at the Most Common Type of Filling Machine
Piston fillers are widely recognized in the packaging industry for their precision and versatility. They operate using a piston mechanism that accurately measures and dispenses a fixed volume of liquid or semi-liquid products.
These machines excel in handling thick, viscous substances such as sauces, creams, and gels. The adjustable speed settings allow for customization based on production needs.
One significant advantage is their ability to maintain consistent fill levels across various container sizes. This reliability reduces waste and enhances product quality.
Piston fillers can easily be integrated into existing production lines. They adapt well to different manufacturing environments, making them ideal for small businesses and large-scale operations alike.
Cleaning is straightforward since many models have removable parts designed with hygiene in mind. This feature simplifies maintenance while adhering to sanitation standards crucial in food and pharmaceutical industries.
Factors to Consider When Choosing a Filling Mechanism
Choosing the right filling mechanism involves several key factors. Start with the type of product you’re dealing with. Is it a thick paste or a thin liquid? The viscosity will greatly influence your choice.
Next, consider production speed. If you need high-volume output, pressure fillers might be more suitable than gravity fillers. Think about how quickly you want to fill each container.
Also, assess the level of precision required for your operation. Piston fillers excel in accuracy, making them perfect for products that require exact measurements.
Don’t overlook budget constraints either; some systems are more cost-effective upfront but may have higher maintenance costs later on.
Evaluate available space in your facility. Some machines occupy more floor area than others, which can affect layout and workflow efficiency.
Case Studies: Real-Life Examples of Businesses Using Different Filling Mechanisms
A small craft brewery in Oregon turned to gravity fillers for its unique beer styles. This method allowed them to gently fill bottles without introducing excess oxygen, preserving the fresh flavors they cherished.
In contrast, a large cosmetics manufacturer opted for pressure fillers. With high demand and varied product viscosities, this mechanism ensured consistency and speed during their production runs. They could easily switch between different formulas without compromising quality.
Meanwhile, an artisanal hot sauce company found success with piston fillers. The precise volume control enabled them to maintain uniformity across their diverse range of spicy sauces while minimizing waste.
These examples illustrate how businesses tailor their filling mechanisms based on specific needs and products. Each method offers distinct advantages that align with the goals of these companies in various industries.
Conclusion: Making the Best Decision for Your Business Needs
Choosing the right filling mechanism is crucial for any business involved in packaging liquids, creams, or semi-solids. Each type of filler—gravity, pressure, and piston—has its unique strengths and weaknesses.
Gravity fillers are often the simplest option; they rely on gravity to dispense products into containers. This makes them suitable for thin liquids but less effective for thicker formulations.
Pressure fillers use air pressure to push product into containers. They excel with high-viscosity fluids but can have a steeper learning curve due to their complexity.
Piston fillers are versatile machines that can handle a wide variety of products, including those with particulates or thick consistencies. Their precision in volume control provides an advantage when exact measurements are essential.
When making your decision, consider factors such as product viscosity, desired speed of production, budget constraints, and the level of automation you require. Analyze how each filling method aligns with your operational needs and goals.
Real-life case studies illustrate how businesses successfully leverage these technologies based on their unique challenges. Learning from others’ experiences can provide valuable insights that guide your choice.
Selecting the right filling mechanism will enhance your production efficiency and meet customer expectations effectively.