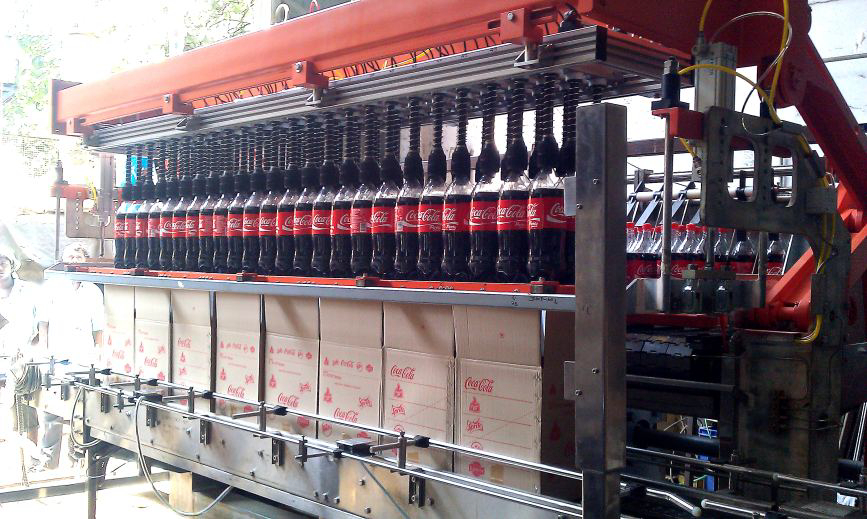
Introduction to PET Filler Machines
In the fast-paced world of manufacturing, efficiency and precision are crucial. Enter PET filler machines—an essential piece of equipment in the beverage and packaging industries. These machines streamline the filling process, ensuring that every bottle is filled accurately while maintaining high production rates. As businesses strive to meet increasing demand, understanding how PET filler machines work can be a game-changer.
Whether you’re new to this technology or looking to upgrade your existing setup, grasping the features and benefits of these machines will empower you to make informed decisions for your business. Let’s dive into what makes PET filler machines so vital for modern production lines.
Types of PET Filler Machines
When it comes to PET filler machines, there are several types tailored for specific needs. Gravity fillers rely on the force of gravity to dispense liquids into bottles. They’re simple and economical, making them a popular choice for low-viscosity products.
Pump fillers use a more controlled method, perfect for thicker liquids. These machines ensure precision in filling volumes and work well with viscous substances like sauces or creams.
Pressure fillers operate by applying pressure to fill containers quickly. This type is ideal for carbonated beverages as they help maintain carbonation levels during the filling process.
Electronic volumetric fillers offer advanced technology that measures fluids accurately using sensors. This ensures consistency and reduces waste across production runs, appealing to businesses focused on efficiency and quality control. Each type serves unique purposes within various industries, enhancing overall operational capabilities.
Key Features of PET Filler Machines
PET filler machines come packed with features that set them apart in the packaging industry. One standout characteristic is their precision filling capability, ensuring each bottle receives an exact amount of liquid. This accuracy not only reduces waste but also enhances product quality.
Another key feature is their versatility. Many PET fillers can handle a variety of container sizes and shapes, making them suitable for different production needs.
Speed is another significant advantage. These machines are designed to operate at high speeds, allowing manufacturers to increase output without sacrificing quality.
User-friendly interfaces make operation easier for staff, reducing training time and minimizing errors during production runs.
Additionally, advanced automation technologies optimize workflows by streamlining processes from filling to capping, which leads to increased productivity across the board.
Benefits of Using PET Filler Machines
PET filler machines offer a range of advantages that can transform production lines. They enhance accuracy by ensuring precise measurements, which minimizes waste and reduces costs.
Speed is another notable benefit. These machines operate at high volumes, allowing businesses to meet demand efficiently without sacrificing quality. Faster filling also contributes to quicker turnaround times.
Consistency is key in any manufacturing process, and PET filler machines deliver just that. They maintain uniformity across all bottles or containers, which helps build brand trust with consumers.
Moreover, automation leads to less manual labor involvement. This not only streamlines operations but also improves worker safety by reducing the potential for injury related to repetitive tasks.
Modern PET filler machines are designed for versatility. They can handle various container sizes and shapes while adjusting swiftly between different products—a critical advantage in today’s dynamic market landscape.
How PET Filler Machines Improve Production Efficiency
PET filler machines significantly streamline the production process. They automate filling tasks, reducing the need for manual labor. This leads to faster operation times and less human error.
Moreover, these machines are designed for precise measurement. Accurate fills mean reduced waste of materials and optimized resource usage. With consistent performance, businesses can maintain quality standards while increasing output.
Another key aspect is their adaptability. Many PET filler machines can handle various bottle sizes and shapes without extensive downtime during changeovers. This versatility allows manufacturers to respond quickly to market demands.
Incorporating advanced technology further enhances efficiency. Features like speed control and automatic cleaning systems minimize interruptions in production cycles
With improved workflow management, companies often see a boost in overall productivity levels—making it easier than ever to meet growing consumer needs.
Tips for Choosing the Right PET Filler Machine for Your Business
Choosing the right PET filler machine is crucial for your production line. Start by assessing your specific needs. Consider the type of products you will be filling, as different machines cater to various bottle sizes and shapes.
Next, look into the machine’s speed and output capacity. Higher efficiency can significantly impact your overall productivity. Don’t forget about energy consumption; an eco-friendly option could save costs in the long run.
Review manufacturer reputations and customer feedback. A reliable supplier often provides better support and spare parts availability.
Also, consider automation features that enhance user-friendliness while minimizing errors during operation. This can lead to less downtime and improved quality control.
Keep budget constraints in mind but avoid compromising on essential features just for cost savings. Investing wisely now can pay off with greater returns later on.
Conclusion
Choosing the right PET filler machine can be a game-changer for your production line. With various options available, consider factors such as speed, efficiency, and ease of use. Assess your specific needs and budget constraints to make an informed decision.
Investing in a quality PET filler machine not only enhances productivity but also ensures consistent product quality. By understanding the features and benefits discussed, you can streamline operations while meeting market demands effectively.
The right equipment plays a crucial role in achieving long-term success in business. As you explore different models and manufacturers, prioritize those that align with your operational goals. Embrace innovation to propel your production capabilities forward.