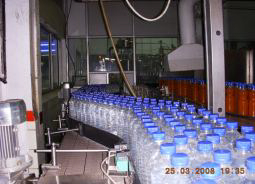
Introduction to Filling Machines
In today’s fast-paced manufacturing world, efficiency and quality are paramount. Filling machines play a crucial role in streamlining production processes across various industries—from food and beverage to pharmaceuticals. Selecting the right filler machine can significantly impact your operational success.
But not all filling machines are created equal. If you’re on the hunt for a high-quality option, it’s essential to know what features will deliver optimal performance and reliability. Understanding these key elements ensures you invest wisely, enhancing productivity while maintaining product integrity.
Let’s dive into five vital features that should be at the top of your checklist when searching for a top-notch filler machine. These insights will help guide you toward making an informed decision that elevates your production line to new heights.
The Importance of Choosing a High-Quality Filler Machine
Selecting a high-quality filler machine is crucial for any production line. It directly impacts efficiency, product quality, and overall operational costs.
A reliable filler ensures that each container is filled accurately. This precision minimizes waste and enhances customer satisfaction by delivering consistent products.
Investing in superior technology also means fewer breakdowns and disruptions. High-quality machines tend to have better durability, which translates into long-term savings on repairs and replacements.
Furthermore, the right filling machine can adapt to various product types and sizes. This versatility allows businesses to remain competitive as market demands change.
Choosing wisely now will lead to greater returns down the road. Quality equipment supports smoother operations and builds a strong reputation within your industry.
Key Feature 1: Accuracy and Precision
When it comes to filling machines, accuracy and precision are non-negotiable. These features ensure that every container is filled consistently, reducing waste and maximizing efficiency.
High-quality filler machines are engineered with advanced technology. This means they can dispense exact volumes of liquid or other materials without the risk of overfilling or underfilling.
Investing in a machine with precise calibration allows for better quality control. Businesses can guarantee that their products meet regulatory standards while also satisfying customer expectations.
Moreover, accurate fillers contribute to cost savings. They minimize product loss during the filling process, allowing companies to maintain profit margins even when operating at scale.
Precision in filling leads not only to operational efficiency but also enhances brand reputation by providing customers with reliable products time after time.
Key Feature 2: Versatility and Adaptability
Versatility and adaptability are crucial when selecting a filler machine. A high-quality machine should handle various products, from liquids to powders, without compromise. Your production line may involve different types of filling tasks.
Machines that can easily switch between container sizes and shapes save time and increase efficiency. This flexibility allows for quick adjustments in fast-paced environments.
Moreover, an adaptable filler can accommodate changes in product formulations or packaging materials. As your business evolves, having a machine that grows with you is invaluable.
Look for features like interchangeable parts or customizable settings. These elements enhance the functionality of the equipment while reducing downtime during transitions.
Investing in a versatile filler ensures your operations remain agile and responsive to market demands.
Key Feature 3: Ease of Use and Maintenance
A filler machine should be user-friendly. Complex machines can lead to frustration and delays. Look for intuitive controls that allow operators to adjust settings quickly.
Maintenance is another crucial aspect. Machines with accessible parts simplify routine checks and cleaning. Regular maintenance ensures consistent performance, extending the machine’s lifespan.
Opt for models that come with clear manuals or online support resources. This access helps your team troubleshoot issues without extensive downtime.
Additionally, consider machinery designed for quick changeovers between products. This feature enhances efficiency when switching from one filling task to another, minimizing interruptions in production flow.
A good warranty and readily available customer service create peace of mind. It shows the manufacturer stands behind their product while offering assistance whenever needed.
Key Feature 4: Durability and Longevity
Durability and longevity are vital when selecting a high-quality filler machine. These machines often operate in demanding environments, facing wear and tear over time.
A robust design ensures that the equipment can withstand heavy usage without compromising performance. Materials should be resistant to corrosion, dents, and scratches, as these factors significantly impact functionality.
Additionally, investing in a durable filler machine reduces long-term costs. Frequent repairs or replacements can quickly drain your budget. A reliable machine minimizes downtime, ensuring productivity remains high.
Look for manufacturers known for their quality standards and warranty offerings. This not only reflects confidence in the product but also assures you of its durability.
Choosing a sturdy filler machine means fewer headaches down the line—an essential consideration for any business aiming to thrive.
Key Feature 5: Safety Features
Safety features are crucial in any filler machine. They protect both operators and the product being filled.
Look for machines equipped with emergency stop buttons. These can halt operations instantly, preventing accidents during unexpected situations.
Additionally, consider models that include safety guards or enclosures. These barriers help keep users safe from moving parts while ensuring a clean work environment.
Automated sensors also play an essential role in safety. They detect misalignments or jams and automatically shut down the machine to avoid damage or injuries.
Ensure that the materials used in construction are food-grade compliant if you’re filling consumables. This guarantees not only safety but also adherence to industry standards. Investing time into understanding these aspects will pay off significantly in protecting your team and maintaining quality control.
Conclusion
When selecting a filler machine for your business, it’s crucial to consider several key features that ensure efficiency and effectiveness. Accuracy and precision are paramount; you want a machine that delivers consistent results with minimal waste. Versatility is another important aspect, as machines that can adapt to different products will save time and increase productivity.
Ease of use cannot be overlooked either. A user-friendly interface along with straightforward maintenance procedures can significantly reduce downtime. Durability plays a vital role in the long-term performance of the machine; investing in robust materials means fewer repairs and longer service life.
Safety features should always be at the forefront of your decision-making process. Machines equipped with proper safeguards protect not only the operator but also enhance overall workplace safety.
Taking these factors into account when searching for high-quality filler machines will set you on the path to optimizing your production line while ensuring quality output across all operations.