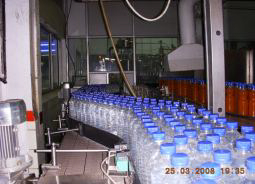
Introduction to Liquid Filling Processes
Liquid filling processes are at the heart of many manufacturing operations, from beverage production to pharmaceuticals. They ensure that products reach consumers in a timely and efficient manner. However, these processes aren’t without their hurdles. Even experienced manufacturers can face obstacles that hinder productivity and compromise quality.
Navigating the intricacies of liquid filling requires an understanding of potential challenges and proactive solutions. Whether you’re dealing with inconsistent fill levels or pesky air traps, recognizing these issues is essential for maintaining smooth operations. Let’s dive into some common challenges faced in liquid filling processes and explore effective strategies to overcome them.
Common Challenges in Liquid Filling
Liquid filling processes are complex and come with their fair share of challenges. Each step in the process requires precision and care to ensure quality.
Inconsistent fill levels often plague production lines, leading to customer dissatisfaction. Achieving uniformity is vital for brand reliability.
Another significant challenge is product spillage or contamination. This can not only waste valuable materials but also compromise hygiene standards. Maintaining cleanliness during filling operations is crucial.
Air trapping presents a unique problem as well, particularly in bottles or containers that require an airtight seal. It can affect product shelf life and overall integrity.
Clogging or blockages within the filling machinery can halt operations entirely, causing delays and increased costs. Regular maintenance helps prevent these issues from arising unexpectedly.
Cleaning and maintaining equipment can be labor-intensive but remains essential for optimal performance over time. These hurdles demand attention to detail at every stage of liquid filling processes.
Issue 1: Inconsistent Fill Levels
Inconsistent fill levels can pose a significant challenge in liquid filling processes. This issue often leads to dissatisfied customers and potential regulatory concerns. When products are not filled uniformly, it creates an impression of poor quality.
Several factors contribute to this problem. Variations in temperature can alter the viscosity of liquids, affecting how they flow during the filling process. Additionally, equipment calibration errors may result in incorrect measurements.
Human error is another culprit; operators might misjudge fill levels during manual processes or overlook automatic settings that need adjustment.
To combat this inconsistency, manufacturers must invest in high-quality machinery equipped with advanced sensors and automation technology. Regular maintenance checks also ensure that all equipment functions optimally, reducing discrepancies in fill levels across batches. Adopting these practices helps maintain product integrity and enhances customer satisfaction over time.
Issue 2: Product Spillage or Contamination
Product spillage or contamination is a critical concern in liquid filling processes. It not only leads to product loss but can also compromise quality and safety. Spilled liquids create hazardous work environments, increasing the risk of slips and falls.
Contamination can occur from various sources—external elements like dust or bacteria, as well as internal factors such as equipment wear. Every point of contact during filling needs scrutiny to ensure cleanliness.
Moreover, spills often disrupt production schedules. Workers spend valuable time cleaning up instead of focusing on efficient operations. Implementing spill containment measures and regular maintenance checks can significantly reduce these risks.
Investing in high-quality equipment with built-in anti-spill technology helps maintain fill accuracy while minimizing the chances for contamination. Ensuring that operators are trained properly further enhances safety protocols throughout the process.
Issue 3: Air Trapping in Bottles or Containers
Air trapping in bottles or containers is a frustrating issue that many manufacturers face. It occurs when air pockets get trapped during the filling process, leading to inconsistent product quality and shelf-life concerns.
These trapped air bubbles can cause oxidation, impacting flavor and potency. This is particularly crucial for sensitive liquids like juices, oils, and pharmaceuticals. The presence of air not only affects quality but also may create pressure build-up in sealed containers.
To combat this problem, implementing vacuum filling technology can be effective. By removing air before sealing, you reduce the likelihood of pockets forming.
Proper container design also plays a role; using shapes that minimize dead space helps ensure smoother filling processes. Regular maintenance on equipment reduces wear and tear that might contribute to air entrapment issues as well.
Issue 4: Clogging or Blockages in the Filling Machine
Clogging or blockages in filling machines can halt production and create significant downtime. This issue often arises from residue buildup, improper materials, or even air bubbles within the system.
When liquids with varying viscosities are involved, the risk of clogging increases. Thicker products may not flow as easily, leading to jams that require immediate attention.
Regular maintenance is crucial to mitigating this problem. Scheduled cleaning sessions help remove any stubborn residues before they become a larger headache. Additionally, using high-quality filters can prevent debris from entering the system.
Training operators on proper handling techniques also plays a pivotal role in reducing blockages. They should be aware of how different materials interact with each other during the filling process.
Investing in advanced machine technology designed to handle diverse liquid types can further enhance efficiency and reduce instances of clogging altogether.
How to Overcome These Challenges
To tackle inconsistent fill levels, consider investing in precision filling equipment. Advanced technologies like load cells or flow meters ensure accuracy in every container.
Preventing product spillage is crucial. Implement containment measures such as drip trays and utilize nozzles designed to minimize overflow. Regularly inspecting these components can also help maintain cleanliness.
For air trapping issues, use vacuum filling methods that eliminate trapped air before sealing containers. This technique enhances both shelf life and product integrity.
Address clogging by scheduling routine maintenance on your filling machines. Clear any potential blockages regularly to keep operations running smoothly without interruptions.
Prioritize ease of cleaning by selecting equipment made from materials that resist corrosion and are easy to disassemble. Streamlined designs significantly reduce downtime during maintenance tasks, allowing for a more efficient workflow.
Conclusion
Liquid filling processes play a crucial role in various industries, from food and beverage to pharmaceuticals. However, these processes often come with unique challenges that can hinder efficiency and product quality. Understanding the common issues—such as inconsistent fill levels, product spillage or contamination, air trapping in containers, clogging in filling machines, and cleaning difficulties—is essential for any operation seeking optimization.
By addressing these challenges head-on with tailored solutions like precise equipment calibration, implementing robust hygiene protocols, utilizing advanced technology for aeration prevention, conducting regular maintenance checks on machinery, and establishing efficient cleaning systems; businesses can significantly enhance their liquid filling operations.
Mastering the art of liquid filling is not just about speed but also precision and cleanliness. By tackling these five common challenges effectively, companies will not only improve their operational efficiency but also build a reputation for quality products that customers trust. Embracing best practices ensures you remain competitive while delivering top-notch results every time.